Dura Baths
These Parts Are Not All The Same
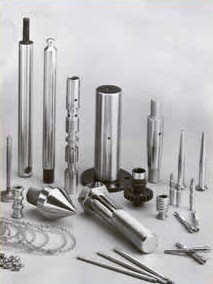
The Dura Bath Additive Is The Difference
Some of these parts were plated in a conventional hard chrome bath and others were plated in a bath using one of the Dura Additives. They may look the same with regards to surface appearance, but there is a huge difference in the quality and structure of the hard chrome deposit.
The ones plated with the Dura additive will far outlast the other ones in service because they have greatly improved metallurgical properties.
These have the benefit of greater hardness, a finer deposit structure, better adhesion, improved fatigue limit, reduced surface friction, less internal stress and better corrosion resistance. This provides a much longer service life on your parts.
To improve your chrome deposit is to improve your business.
Why This Is Important
The life of a single component or an entire assembly depends upon the properties of the hard chrome deposit. Premature failures within this relatively thin layer of chromium can have catastrophic results causing expensive down time and repairs. Manufacturers want the best hard chrome deposit available on their parts. Job shops want to provide their customers with the best quality possible. Both will specify that a Dura Additive is used for their plating because using a Dura bath additive improves the deposit properties.
The Dura additives also provides significant cost savings as they are used with generic chromic acid and there are no expensive proprietary blends to buy.
Dura is the “Next Technology” in hard chrome plating.
Improved Deposit
Some of the benefits of using a Dura additive in your hard chrome baths include:
Property | Standard Bath | Dura -3000 |
Technology: | Old | New |
Crack Type: | macro | ultra micro |
Crack Density (per lineal inch): | 50, typical | 3,000 |
Hardness (RC): | 56-60 | 72-74 |
Friction (static): | 0.16 | 0.12 |
Wear Resistance (Taber grams): | 2.3 | 1.5 |
Surface Finish (micro-nodules): | Rougher | Very Smooth |
Oil Retention : | Fair | Excellent |
Adhesion (psi): | 90,000 | 130,000 |
Fatigue Limit (psi): | 45,000 | 90,000 |
Internal Stress: | tensile | compressive |
Corrosion Resistance (5% Salt Spray): | 2-8 hours | 25-35 hours |
Brightness: | Fair | Excellent |
Throwing Power: | Fair – Poor | Excellent |
Impurity Resistance: | Poor | Excellent |
Deposit Efficiency: | 15-16% | 34-35% |
Deposition Rate(2 ASI): | 0.0007”/hr. | 0.00125”/hr. |
Crack Structures
On the surface, all chrome deposits look pretty much the same, especially after they have been polished. The metallurgical structure of the deposit, however, varies drastically depending upon the type of process used.
Conventional chrome baths produce a microstructure that is quite coarse when viewed under a microscope. This limits the desired properties of the deposit. Chrome deposits produced in a Dura bath, however, show considerable improvement in important areas like hardness, wearability, grain size, and corrosion resistance.
The following photomicrographs shown the difference in deposits plated in a conventional bath and a Dura bath.
Standard Bath
Deposit surface at 100 x magnification.
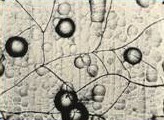
Coarse crack structure from high
internal stress with large nodules & pitting.
Dura Bath
Deposit surface at 100 x magnification.
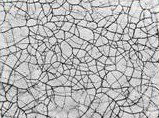
Fine crack structure provides better
oil retention, hardness, wearability and smoothness.
Standard Bath
Deposit surface at 100 x magnification.
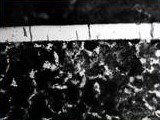
Large deep cracks extend down to
base metal serve as pathways for corrosion.
Dura Bath
Cross Section at 400 magnification
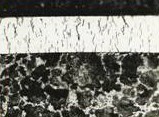
The greater number and smaller sized microcracks provide better lubricity and corrosion resistance.
The Dura Bath Additives complies with Federal Specifications:
QQ-C-320 | ASTM B-177 |
MIL-C-7460 | AMS 2406 |
MIL-C-20218 | AMS 2407 |
MIL-C-23422 | AMS 2438 |
MIL-STD-1501 | BAC 5709 |
DOD-STD-2182 | NAVSHIPS 0919-000-9010 |
MIL-C-23422 |